News & Trends
The Evolution of dvLED: From DIP and SMD to Mini and Micro
With InfoComm 2023 (and > 70 dvLED company exhibitors!) now in the rearview mirror, it is time to clear up what can only be called confusion or obfuscation about dvLED categories and names. We want to take you on a journey through dvLED display technology relative to flat panel displays, starting with LCD. Stay tuned. We will quickly get through LCD and move forward to dvLED, mini-LED, and micro-LED to clear up any latent confusion or misinformation.
LCD displays (both projectors and flat panels) are transmissive. This means they require a light source that shines through the LCD panel to provide the image we see. For flat panels, the beginning was cold cathode fluorescent, aka CCFL. Think of this as a miniature fluorescent tube. As LCD technology evolved, the CCFL backlight was replaced with LEDs, giving a brighter image, longer life, and a more even backlight. There were edge-lit LCD displays for depth and direct-lit versions for performance. The benefit of direct-lit was the ability to dim areas of the picture responding to the video signals and improving contrast.
Now we come to what can only be termed marketing obfuscation. To differentiate themselves in what has realistically become parity in the flat panel market, some LCD panel manufacturers (since they have adopted LED backlights) used to refer to their LCDs simply as LED displays or LED TVs. In short, they are not LED displays. They are LCDs using variations of LED backlighting, which today often incorporates a form of quantum dot technology (and yes, we will explain QD in another article). Now that we have cleared that up, we will focus on dvLED for commercial applications and intentionally avoid going into depth on other variations of more consumer-oriented flat panel displays such as OLED and, more recently, QD-OLED.
LEDs are an emissive technology meaning they create their own light. LED stands for light-emitting diode, a solid-state device that uses semiconductors and the principle of electroluminescence to create light. In short, this is the process of producing light when an electric current is passed through a solid object... in this case, a diode. A dvLED display consists of red, green, and blue LEDs mounted in a fixed pattern. These three colors combine to form a pixel. By adjusting the intensity of each diode, billions of colors can be formed. Looking at the LED screen from a certain distance, the array of colored pixels is seen as a seamless image.
For dvLED displays, it began with DIP (dual in-line package) technology. DIP has been around for over 50 years and is likely what you think of when you picture an LED. DIP LEDs are far from outdated as they are still used extensively today for large outdoor signs and displays. The widespread use of DIP LEDs came about due to their long life-span and intense brightness (upwards of 10,000 nits) in direct sunlight. DIP LEDs are highly recognizable by their "bullet" shaped epoxy dome and the long contacts that extend from the bottom of the LED, which is then soldered or inserted into an electronic circuit board. The LED's epoxy dome serves as a lens that can focus the light coming from the diode.
Next came surface-mounted device (SMD) chips. They have become very popular due to their versatility and size. SMD chips are much smaller than the DIP technology and support chips with more complicated designs; this can mean having RGB capabilities on a single chip, providing very powerful color combinations. The technology does not employ the bullet-shaped design from DIP LEDs, and is closer to that of a tiny, flat, square computer chip. SMD chips have been a significant development for the dvLED display industry because of the ability to put three diodes on the same chip, meaning you can pack them much closer together – meaning finer pixel pitch, higher resolution, and closer viewing distances.
The most recent LED development has been chip-on-board or COB technology. COB and SMD can appear at first glance similar because, like SMD, COB chips have multiple diodes on the same "wafer" or chip. However, this is where the similarities end. In fact, on every COB chip, there are multiple diodes, typically nine or more. The other big difference between COB and SMD technology is that while SMD requires a circuit for every diode included on the chip, COB devices only have one circuit and two contacts for the entire chip regardless of the number of diodes. Regardless of the number of diodes on the chip, this single-circuit design makes any COB LED device simple. Perhaps even more important than the simplicity aspect, COB also leads to improved nits-per-watt ratios compared to other LED technologies such as DIP and SMD.
Now that you know the entry-level basics about DIP, SMD, and COB, we will address the current buzz in the indoor LED display industry… of course, we are referring to both mini-LED and micro-LED.
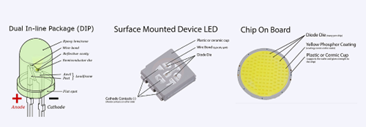
In the era of the UHD 4K flat panel displays as the norm, Mini/Micro LED has greatly improved dvLED specifications and picture quality, and resolution performance. The chip sizes of the two have both been miniaturized. However, mini-LED and micro-LED are technologically different in both pixel size and manufacturing technique... the main difference is that mini-LED is larger and uses a sapphire chip substrate, while micro-LED is smaller in size and does not require a sapphire substrate. The dimensions of a mini-LED chip are between 100~300μm, whereas micro-LED chips are less than 100μm in size; both use flip-chip packaging to build display-ready products through what is known as mass transfer. Relax, we won't go any deeper than that!
Mini-LED (aka "sub-millimeter light emitting diode," if you want to be precise) began its commercial display lifespan as a smaller LED, about 100 micrometers or a fifth of the size of a standard LED. This is a much-improved version of traditional SMD LEDs originally used for LCD backlights. That smaller size means more of them can be packed together in the same area, allowing a full array backlit LCD display to offer hundreds (or more) of discrete dimming zones to enhance contrast and improve black levels.
However, mini-LED applications are evolving beyond the screen size limitations of LCD (approximately 120" max). They are now being used for indoor dvLED displays in applications such as conference rooms, control rooms, and high-end digital signage where fine pitch is required. LEDs smaller than 0.2 millimeters are said to be mini-LED. They are usually from P1.2 down to P0.6 pixel-pitch.
Not to be confused with mini-LED, micro-LEDs (aka. microLED, mLED, or μLED) are even tinier and offer higher performance. It wouldn't be until the year 2000 that the first inorganic micro-LED would be developed, and it would still take another nine years for this product to be patented for display purposes. Current micro-LED sizes are smaller than 50μm — less than 0.002 inches across — making them less than 1/100th the size of a conventional LED. As one expert notes, "That is small enough to serve as a single pixel in conventional TV sizes and resolutions, and that's where micro-LED gets really interesting. If mini-LED provides a refinement on the existing LCD backlight, MicroLED promises to be more revolutionary, offering a technology that can go head-to-head with OLED and win, with better brightness and more vivid color."
Micro-LED display performance is often compared to OLED displays - the current premium emissive consumer display technology. OLEDs use tiny sub-pixels made from organic emissive materials. MicroLEDs are somewhat similar - but with an inorganic LED structure. Compared to OLEDs, micro-LEDs promise to be much more efficient and brighter, more durable (longer lifetime), and with a wider color gamut, mostly due to the superior performance of inorganic LEDs over their organic counterparts. The inorganic nature of micro-LEDs gives them a longer lifetime advantage over OLEDs and allows them to display brighter images with minimal risk of screen burn-in. The sub-nanosecond response time of micro-LED has a huge advantage over other display technologies for applications such as 3D/AR/VR displays since these devices need more images, more pixels per image, more frames per second, and fast response.
The main drawback of micro-LED technology is that it is not yet mature, and there are still challenges on the path towards full commercialization, as current production costs are extremely high. Micro-LEDs, while amazing for brightness and picture quality, are incredibly tedious and costly to manufacture into a display. Even with the latest in robotic technologies, manufacturing micro-LED displays remains very time-consuming and costly, meaning a micro-LED display will be more expensive in the near and midterm than a similar COB or mini-LED display.
When discussing mini-LED and micro-LED, a very common feature to distinguish between the two is the LED package size. As the names indicate, mini-LEDs are considered LEDs in the millimeter range, while micro-LEDs are in the micrometer range. However, the distinction is not so strict in reality, and the definition may vary from company to company. Today, it is commonly accepted that micro-LEDs are under 100 µm size and even under 50 µm, while mini-LEDs are much larger. The differences between mini-LEDs and micro-LEDs determine their ease of realization and degree of technology maturity.
This begs the question of where we are regarding micro-LED. We know that over 130 companies (and more on the way) are involved in micro-LED research and development. Companies like Samsung, Sony, LG, Leyard, and most recently, AOTO among others, have shown micro-LED displays at .3mm and others in prototype form down to 0.13mm. Micro-LED displays in the 0.4mm to 0.5mm range are commercially available today.
This is a look into the current state of affairs and a peek into the foreseeable future, but where we are today in dvLED for most indoor commercial applications resides firmly in SMD, COB, and mini-LED displays in the 1.5mm down to .7mm pixel pitch categories. The goal of dvLED (or any digital display technology) is to avoid seeing discrete pixels on screen, and this is by the laws of physics and visual acuity, a function of pixel pitch and viewing distance. Finally, keep top of mind as you design a project that the smaller the pixel pitch, the higher the price, so design your projects and buy what your viewing distance dictates.